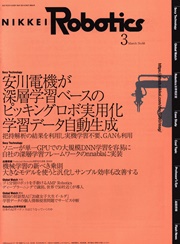
- 니케이로보틱스_2021/3_이온그룹 물류거점에서 피킹 지원 로봇 가동 NIKKEI Robotics
-
- 저자 : 日経BP社
- 발행일 : 20210210
- 페이지수/크기 : 39page/28cm
요약
Nikkei Robotics_2021.3 Cool Topic (p24-29)
이온그룹의 물류거점에서 피킹 지원 로봇 가동
게이요유통창고가 펫 용품 출하에 도입, 효율 2배로
물류현장에서 사람과 협동해 피킹을 효율화하는 로봇의 활용이 확산되고 있다. 간토지역을 거점으로 물류사업을 전개하는 게이요(京葉)유통창고는 대형 유통기업인 이온(AEON)그룹의 물류거점에 피킹 지원 로봇 ‘AMR(Autonomous Mobile Robot)’을 도입. 2020년 11월 말부터 사이타마시 이와쓰키영업소에서 20대를 가동시켰다. 펫 용품을 점포 별로 출하하는 업무에 적용하고 있다. AMR은 상품 선반을 차례로 돌면서 작업자가 피킹한 상품을 접이식 컨테이너에 실어 자동 운반하고 있다.
게이요유통창고는 출하량이 증가하면서 업무를 효율화하기 위해 로봇을 도입했다. 이와쓰키영업소 주변에 많은 물류창고가 건설되고 있어 작업자를 확보하기가 어려워진 것도 한 요인이다. 로봇 활용을 통해 기존의 노동력에만 의지한 작업과 비교해 1시간당 피킹 효율이 약 2배로 향상되는 등 효과가 나오기 시작했다.
-- 50L 접이식 컨테이너 2개가 필수조건 --
이와쓰키영업소에서는 펫 용품 전문상점에서 발송 업무를 하청 받고 있고, 펫 푸드 등 약 1만 2,000개의 상품을 취급한다. 이온그룹의 펫 전문점이나 슈퍼 등 점포 별로 피킹해 각 사의 물류거점에 발송하고 있다. 출하처 매장은 1,000개 이상이며, 많은 곳에서는 한 점포당 2~3개의 접이식 컨테이너를 매일 출하하고 있다. 이번에는 이들 업무의 20~30%를 AMR로 효율화했다. 투자액은 약 8,000만 엔이다.
지금까지 AMR은 주문 1건당 상품 수가 적은 개인용 EC의 발송 거점에서 도입되는 경우가 많았다. 일반적으로 AMR은 좁은 통로에서도 주행할 수 있도록 소형이 많고, 너무 많은 상품이나 대형 상품은 실을 수 없었기 때문이다. 게이요유통창고처럼 1건당 상품 수량이 많은 업무에 AMR을 적용하는 예는 흔치 않다.
게이요유통창고는 처음부터 AMR 도입을 검토했던 것은 아니었다. 18년 무렵에는 당초 3억엔 정도의 예산으로 선반 운반형 로봇 도입을 검토하고 있었다. 19년도 경제산업성의 보조금사업 ‘지역경제 견인사업지원 사업비보조금’에 채택된 계획을 추진하고 있었지만 발주 직전에 단념했다. “히타치제작소의 Racrew나 중국 Geekplus Technology의 로봇을 검토하고 있었는데, 이들 선반 운반형 로봇은 새로 창고를 빌리고 선반도 전용 선반으로 교체해야 하는 등 대규모 개혁이 필요했었다”(게이요유통창고 DX추진실 이즈카(飯塚) 실장).
이즈카 실장이 도입에 주저하고 있을 무렵, 때마침 물류업계에서는 AMR 발표가 이어졌다. 선반 운반형 로봇 개발업체인 GROUND도 AMR을 발표하고 전시회 등에서 이를 공개했다. Rapyuta Robotics도 일본유통과의 실증실험을 막 시작한 시점이었다.
이즈카 씨는 GROUND의 쇼룸을 찾아가 AMR이라면 자사의 창고에서도 활용할 수 있겠다는 느낌을 받았다. 그러나 GROUND의 로봇은 당시 EC용을 전제로 하고 있었기 때문에 실을 수 있는 상품의 양이 적다는 것이 과제였다. 마침 그때 이와쓰키영업소 근처에서 로봇 PR이벤트를 진행하고 있던 Rapyuta Robotics와 만났다. 그리고 “50L 접이식 컨테이너 2개를 로봇에게 실을 수 없을까?”라고 물었다.
Rapyuta Robotics는 당시 일본유통을 위한 로봇을 개발하고 있었고, 공조기기 업체의 보수용 부품과 같은 작은 부품을 대상으로 하고 있었다. 그 때문에 Rapyuta Robotics의 AMR은 용적이 20L 정도의 작은 상자를 2개 싣는 것이 한계였다. 예전부터 물류업계의 이러한 수요를 파악하고 있던 Rapyuta Robotics는 이즈카 씨의 질문이 계기가 돼서 하드웨어를 개조해 50L의 대형 접이식 컨테이너를 실을 수 있도록 했다.
-- 빈도가 높은 상품을 로봇으로 --
이와쓰키영업소에서는 1만 2,000개의 상품을 다루고 있지만 절반은 펫 푸드 등 작은 상품이다. 출하 빈도 별로 6개의 구역으로 나눠서 구역 단위로 피킹을 실시하고 있다. 이 중에 가장 출하 빈도가 높은 4개의 구역, 약 6,000 종류의 상품에 AMR을 적용했다. 기존에는 피킹 작업에 50~60명을 할당하는 등 가장 노동력을 요하는 작업이었다. 남은 2개 구역의 상품은 지금도 사람이 피킹하고 있다. 펫 기저기나 대용량 사료 등의 대형 상품은 별도의 구역에서 지게차 등을 사용해 출납하고 있다.
AMR은 상품을 운반하는 기능을 갖추고 있지만 가장 중요한 상품 피킹 자체는 사람이 해줘야 한다. 그렇다고 해서 사람이 항상 AMR과 같이 행동한다면 사람이 걷는 거리가 너무 길어지게 된다. 기존형 카트가 전동화된 정도의 효과밖에 얻지 못했다. 이 때문에 AMR을 효율적으로 운용하기 위해서는 AMR과 사람을 각각 독립적으로 운용∙스케줄링하는 것이 포인트가 된다. 로봇의 행동 루트는 IT시스템에서 자동 생성할 수 있으므로, 특히 초점은 사람을 구역 내에 어떻게 배치하고 움직이게 할 것인가다.
방식은 주로 2개다. 하나는 ‘존(Zone) 방식’이라는 것이다. 특정 구역에 작업자를 국소적으로 배치한다. 작업자는 담당 구역 내에 로봇이 오면, 그 로봇에 해당 상품을 담는다. 존 방식은 상품이 출하 빈도에 상관없이 똑같이 분산돼 보관되고 있는 경우에는 유효하지만 게이요유통창고처럼 출하 빈도 별로 상품을 보관하고 있는 경우에는 적합하지 않다. 출하 빈도가 낮은 구역에 있는 작업자 밑에는 로봇이 거의 오지 않기 때문이다. 또한 존이 넓으면 담당 구역 내에 로봇이 와도 작업자가 알아차리지 못하는 경우도 있다.
그래서 게이요유통창고는 다른 방식인 ‘가이드 방식’을 채용했다. 작업자를 특정 구역에 고정 배치하는 것이 아니라, 1회 피킹을 마치면 다음 피킹 장소가 로봇 화면에 표시된다. 작업자는 그 지시에 따라서 복수의 구역 전체를 커버한다. 로봇 20대에 8~10명의 작업자를 할당했다. 또한 게이요유통창고는 작업자가 창고 내의 선반 위치를 숙지하고 있기 때문에 로봇 화면에는 지도 상의 위치가 아니라 선반 번호만을 표시하도록 했다.
가이드 방식은 존 방식처럼 많은 작업자를 배치할 필요는 없지만 작업자의 부담이 경감되기는 어렵다. 걷는 범위가 모든 구역에 걸쳐있어 보행거리가 길어지기 때문이다. 게이요유통창고는 어디까지나 피킹 속도를 우선했다고 한다.
가이드 방식의 경우는 사람에 따라서 하루 보행거리가 다르다는 문제도 있다. 그래서 Rapyuta Robotics는 각 작업자가 걷는 거리를 평준화하는 대응도 추진하고 있다고 한다. 작업자마다 보행거리를 시스템 측에서 파악할 수 있도록 하고, 그 결과를 바탕으로 다음 피킹 장소를 지시하도록 한다.
소정의 상품을 모두 실은 로봇은 구역 내의 외주에 있는 롤러 컨베이어로 접이식 컨테이너를 운반한다. 컨베이어 위로 옮기는 작업은 근처에 있는 작업자가 한다. 컨베이어 근처에서 피킹을 마치면 로봇의 터치패널에 선반 번호 대신에 컨베이어로 옮기도록 지시가 나온다.
-- 안전을 고려해 개수 공사 실시 --
로봇 가동 구역에서는 기존 방식대로 사람도 같이 작업을 한다. 또한 큰 통로에서는 입하 작업 등을 하는 지게차도 왕래한다. 이 때문에 충돌을 방지하는 등 안전을 확보하기 위한 대책도 실시했다.
예를 들면, 로봇의 행선지를 주위 작업자들이 알 수 있도록 통로를 돌아갈 때는 방향 지시기로 알리거나 터치패널에 목적지와 주행 루트를 표시하도록 했다.
또한 로봇이 지게차가 왕래하는 큰 통로를 지나가지 않아도 되게끔 수백만 엔을 들여 개수 공사를 실시했다. 원래 각 구역은 벽으로 구분되어 있었기 때문에 로봇이 다른 구역으로 이동할 때는 한번 구역 밖으로 나갔다가 큰 통로를 주행해 다른 구역으로 들어가야 했다. 그래서 각 구역을 구분하는 벽을 일부 제거해서 구역 사이를 직업 왕래할 수 있도록 했다. 또한 작업자도 큰 통로를 지나지 않고도 구역 사이를 왕래할 수 있어 작업 효율이 향상되었다.
-- 하단의 접이식 컨테이너를 서랍으로 --
로봇에게는 2개의 접이식 컨테이너를 실을 수 있다. 하단에는 상품을 쉽게 넣을 수 있도록 앞으로 당길 수 있게 했다. 서랍에는 잠금 기구를 만들어서, 상품을 잘못 넣는 실수를 방지하는 대책도 되고 있다. 잠금은 하단의 접이식 컨테이너에 상품을 넣는 주문이 있을 때만 해제한다. 상단의 접이식 컨테이너용 상품을 잘못해서 하단 컨테이너에 넣는 일을 방지할 수 있다.
접이식 컨테이너에 넣는 상품은 사전에 로봇 시스템 측에서 전체 용적이나 질량을 계산한다. 게이요유통창고의 창고관리시스템(WMS)에는 원래 상품의 크기나 질량 정보가 등록되어 있지 않았기 때문에 도입할 때 이들을 계측했다. 게이요유통창고의 종업원 2명이 물류용 계측기를 사용해 2개월 동안 6,000 종류의 상품 전체를 계측했다고 한다.
-- 끝 --
Copyright © 2020 [Nikkei Robotics] / Nikkei Business Publications, Inc. All rights reserved.
목차